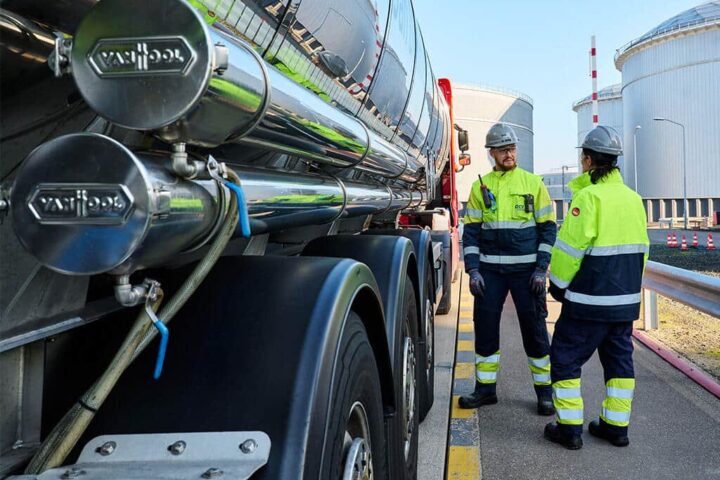

Leading European producer and distributor of ammonia, nitrate fertilizers and hydrogen products and solutions
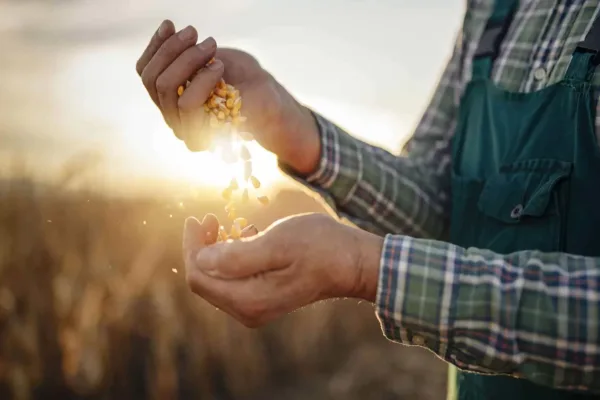
Agricultural Solutions
Ammonia, nitrate fertilizers, and other nitrogen-based solutions.
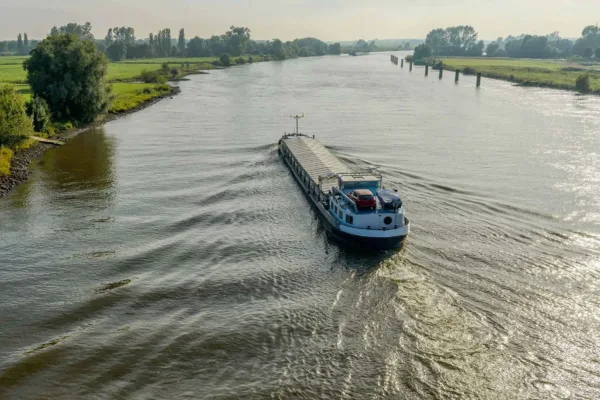
Industrial Solutions
Decarbonizing the energy-intensive industries that shape, feed and fuel our world.
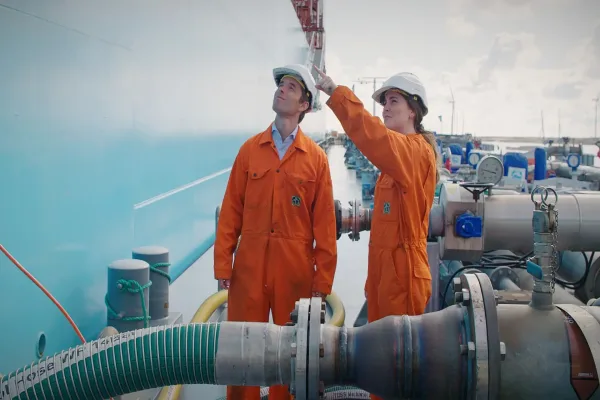
OCI Global Annual Report
Read about our progress towards a cleaner future in our 2024 Annual Report.